Chemical Fiber Industry Automated Storage Retrieval System ASRS Solution
Place of Origin | China |
---|---|
Brand Name | Kinte |
Certification | ISO9001/FEM/ISO14001/OHSAS 18001 |
Model Number | Customized |
Minimum Order Quantity | Negotiable |
Price | Negotiable |
Packaging Details | Packed with plastic films and wrap with strips |
Delivery Time | According to customer's requirement |
Payment Terms | Negotiable |
Supply Ability | Strong production capacity |
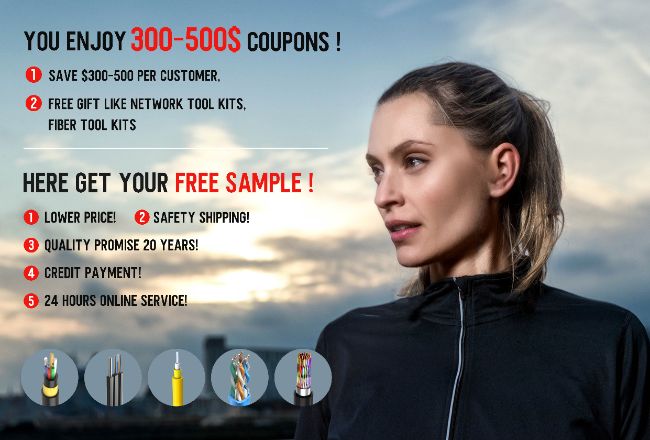
Contact me for free samples and coupons.
Whatsapp:0086 18588475571
Wechat: 0086 18588475571
Skype: sales10@aixton.com
If you have any concern, we provide 24-hour online help.
xReliability | High | Operate & Maintain | Easy |
---|---|---|---|
Industry | Chemical Fiber Industry | Operate | Easy |
Maintain | Easy | Monitoring Machine | MC |
Main Management Calculation | HCl | ||
High Light | MC Automated Storage Retrieval System,HCl ASRS Automated Storage Retrieval System,MC HCl Automated ASRS Solution |
Chemical Fiber Industry Automated Storage Retrieval System ASRS Solution
Chemical Fiber Industry Intelligent Storage System MHS ASRS
Features of warehouse control system
The control system is a layered distributed computer system, which consists of a management layer, a monitoring layer, a control layer and a device layer, and has the following characteristics:
High reliability
In the system, the double-layer backup of the main management machine, the white check function when the system is started, the anti-interference measures in software, and the far-infrared and optical fiber communication are all effective measures to improve the reliability of the system and make the system run stably.
Easy to operate and maintain
The man-machine interface of this system is clear and simple, and there are concise prompts and operating procedures for system operation and maintenance.
Warehouse Operation Process
Inbound operation process
The palletizer of the automatic grading and packaging line stacks the finished filament products packed in cartons on the empty pallets in three layers of five or six boxes per layer, and then sends them to the conveyor of ASRS to start the storage operation.
When the goods pass the inbound barcode reader, the pallet number is scanned and passed to the main management calculation HCl, HCl compares the pallet number with the pallet information it received from the packaging line, if there is information about the pallet, and there is no blind code (barcode information cannot be read), then HCl will allocate the inbound addresses according to the principles of uniform distribution, closeness to the outbound exit, and priority of high-numbered lanes, and then send the allocated address information and operation commands to the monitoring computer. mc.
The monitoring machine MC sends the pallet number and the roadway number of its storage to the storage fork bar code system, the control system sends the storage tray to the designated aisle conveyor according to the operation order, and the bar code system sends the information of the forked pallet. to MC. According to the information returned by the fork bar code system, the MC eliminates the forked pallet number in the fork queue, and communicates with the corresponding stacker controller to issue the order of the warehousing operation in sequence. The stacker carries out the corresponding warehousing operation.
After the stacker completes the warehousing operation, it returns information such as job completion to the MC, and waits for the next job command. MC returns information such as job completion to HCl for warehousing and registration management, and the system has relatively complete protection measures for the safe operation of the system. If the stacker fails. -MC automatically sends out the "fault stop" stacker command, and carries out the corresponding troubleshooting. When delivering a fault that is difficult to recover immediately, the MC will automatically notify the HCI of the information, and the HCI will do "sealing management", and will no longer allocate warehousing goods to the faulted aisle.
HCl will not assign an inbound address to the blind-coded goods (pallets) when the inbound barcode reader displays the Yuma code. After the pallet is processed and inspected by the manual trolley, it is put into storage from the blind code processing section conveyor. When there is a blind code in the fork bar code of the warehouse, it is also put into the warehouse through the manual trolley, and HCl compares its pallet number. The lower-level system sends the inbound data D. There is a height limit device in the corresponding section of the inbound conveyor to limit the super high goods after manual processing.
Design Specification | Project Result |
Racking system + conveyor line
|
Realize the functions of automatic cargo storage, precise picking and return to storage, etc., greatly improving efficiency and accuracy while reducing labor. |